HWA-HSIA
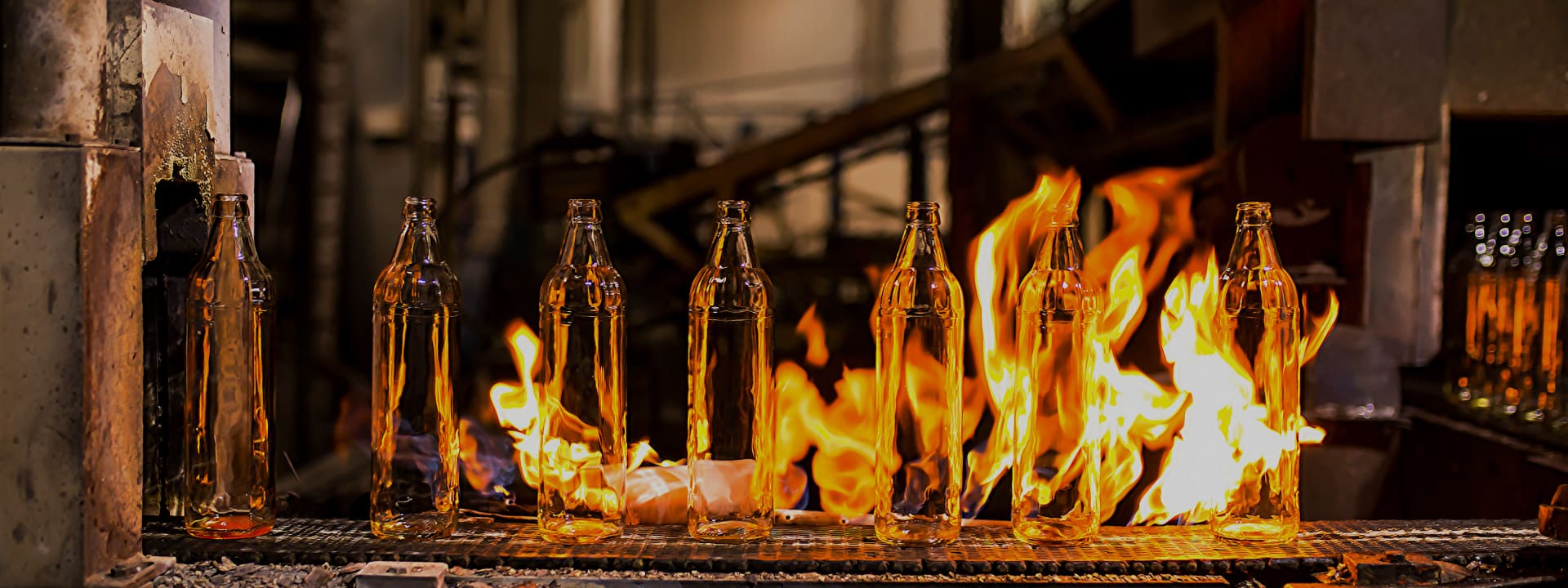
Company News
How Glass is Made Step by Step – From Sand to Custom Glassware
Glass surrounds our daily lives—from the drinking cup in your hand to the jars in your kitchen. But what is glass made of, and how are glass jars made?
In this article, we’ll explore what glass is made from, what it’s composed of, and how glass is made step by step. You’ll also get a behind-the-scenes look at glass production and processing at Hwa Shia—a glass manufacturer with over 100 years of experience in perfecting the craft.
What is Glass Made Of?
Glass might look simple—but it’s made through a carefully balanced mix of ingredients, each playing a vital role in shaping its strength, clarity, and durability.
At Hwa Hsia Glass, our standard glass formula includes:
- Silica Sand (SiO₂) – About 70% of our raw material comes from high-purity silica sand, the key to creating clear and strong glass.
- Soda Ash (Na₂CO₃) – Helps lower the melting point of silica, making the production process more energy-efficient.
- Limestone (CaCO₃) and Dolomite (CaMg(CO₃)₂) – These stabilize the glass structure, improving durability and resistance to water and chemicals.
To ensure quality, we go beyond the basics:
- We process and purify our own glass cullet (recycled glass) in-house—cleaning and removing contaminants to make sure it’s suitable for remelting and reuse.
- While we don’t add specialty chemicals during the raw material stage, we apply a protective coating during quality control. This anti-scratch surface treatment improves durability and reduces damage during shipping and handling.
This combination of high-quality raw materials and thoughtful finishing processes is what makes Hwa Hsia’s glass clear, strong, and reliable—ready to serve industries from food to beauty to wine.
How Is Glass Made: Step-by-Step
Behind every clear bottle or jar is a precise and controlled process.
At Hwa Hsia Glass, we follow a standardized, six-step production flow to ensure high-quality results for every product:
1. Material Batching – Precision Starts Here
Glass begins by carefully weighing and mixing raw materials such as silica sand, soda ash, limestone, dolomite, and recycled glass (cullet).
At Hwa Hsia, this process is fully automated using smart batching machines to ensure that every batch maintains consistent proportions—a critical factor for strength, color, and clarity.
2. Melting – Turning Solids into Liquid Glass
The raw mix is then fed into a furnace and melted at extremely high temperatures—typically above 1,400°C.
While our furnace operation is similar to most manufacturers, we maintain strict controls and regular monitoring to keep the melt quality stable. The molten glass is then ready to be shaped.
3. Molding/Forming – Tailored by Product Type
Depending on the product, the molten glass goes through different forming techniques:
- Glass Cups → Mold-pressed
- Glass Bottles → Blow molding or press-blow
- Glass Jars → Custom-molded for branding or unique shapes
This ensures every item not only meets function and durability needs but also supports product design goals (such as grip, pourability, or shelf appeal).
4. Annealing – Strengthening Through Controlled Cooling
Once formed, the hot glass enters an annealing lehr—a long tunnel-like oven where it's cooled down gradually and evenly.
This slow cooling process relieves internal stresses and prevents cracking or warping over time, which is especially important for packaging used in food, wine, or beauty products.
5. Finishing – Surface Treatment and Decoration
After cooling, the glass can undergo various finishing processes like:
- Anti-scratch surface treatment to boost durability during transportation
- Custom printing, polishing, or frosting based on brand requirements
This step adds both function and aesthetics to the final product.
6. Quality Inspection – Every Piece Checked, Twice
At Hwa Hsia, we take quality control seriously:
- During production, on-site operators conduct regular in-line inspections
- After production, the quality assurance (QA) team performs final checks before packaging
- If any defects are found, the QA team immediately communicates back to the production line for fast adjustments
This two-tiered inspection system ensures that every piece leaving our factory meets your specifications—no surprises, just dependable quality.
Sustainability in Glass Production
As global industries shift toward greener manufacturing and ESG accountability, Hwa Hsia is also actively integrating practices that reduce waste, lower emissions, and support a circular economy.
1. High Cullet Usage – Closing the Glass Loop
One of the most impactful ways to reduce energy and carbon in glassmaking is by using cullet—crushed recycled glass—instead of virgin raw materials.
At Hwa Hsia, certain furnace lines run with up to 65% cullet content, significantly reducing:
- Melting energy consumption (since cullet melts at a lower temperature)
- Raw material mining
- CO₂ emissions per ton of glass produced
We’re also investing in internal cullet cleaning processes, ensuring glass scraps are properly washed and sorted to meet food- and cosmetic-grade safety standards.
This internal loop reduces material waste and supports clients seeking eco-conscious packaging.
2. Smart Monitoring for Smarter Energy Use
While traditional glass manufacturing is energy-intensive, Hwa Hsia is exploring and gradually implementing smart monitoring systems to enhance efficiency. Although still under development, our internal trials of automated production control aim to:
- Optimize furnace performance through temperature stability
- Track real-time energy usage and pinpoint areas of high consumption
- Reduce excess heat waste by refining forming and annealing processes
This sets the stage for future data-driven energy-saving upgrades, aligning with industry 4.0 trends.
3. Toward ESG & Net-Zero Goals
We recognize that sustainability today goes beyond operations—it requires a clear and accountable vision. Hwa Hsia is currently drafting its first formal ESG strategy, which includes:
- Increasing cullet use across all product lines
- Benchmarking energy and emissions data for improvement
- Exploring future alignment with net-zero manufacturing standards
While we haven’t yet pursued third-party sustainability certifications, these initiatives represent our proactive step toward greener production and transparent responsibility.
Let’s Build Better Glassware Together
From high-purity silica sand to cullet-rich sustainable batches, Hwa Hsia combines precision engineering with eco-conscious manufacturing to produce glassware that meets the highest standards in clarity, durability, and sustainability.
Whether you're launching a new product line or upgrading to greener packaging, we offer customized solutions backed by decades of experience.
Want to design your own premium glass container—or explore sustainable options?
Contact us today for a free consultation tailored to your needs!
FAQs
What is glass made of?
Glass is mainly made from silica sand, combined with soda ash, limestone, and sometimes recycled glass (cullet).
How is glass made step by step?
- Raw materials are measured and mixed.
- The batch is melted in a furnace.
- Molten glass is formed into shape.
- Glass is slowly cooled (annealed).
- Surfaces are treated or printed.
- Products go through strict quality checks.
How does sand become glass?
At high heat (about 1400°C), silica sand melts and fuses with other ingredients to form liquid glass, which is then shaped and cooled into solid glass.
What is the raw material of glass?
The main raw material is silica sand, supported by soda ash, limestone, and often recycled glass to reduce waste and energy use.